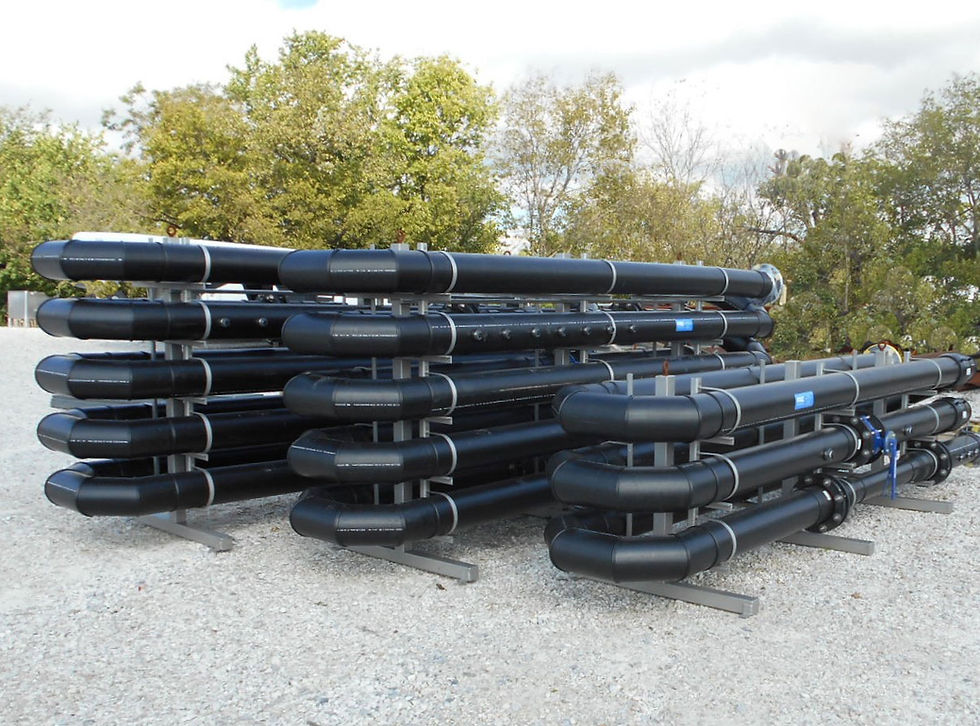
Flocculators, both Plug-Flow Reactors (PFR) and Continuous-Stirred Tank Reactors (CSTR), provide the mixing action and retention time required to chemically treat wastewater. Chemical treatment includes coagulation, pH adjustment, and flocculation. Coagulants are used to break the emulsions in the wastewater and form micro-flocs. Flocculation through polymers is used to agglomerate the coagulated particles creating macro-flocs that can be easily removed by dissolved air flotation (DAF).
As with all FRC systems, our engineers meticulously design each element of our flocculators, making them arguably the best performing chemical reaction vessels on the market.

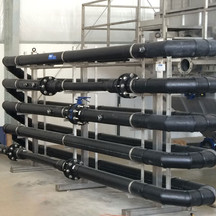
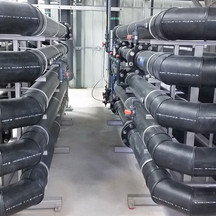



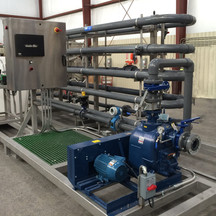

Compact Footprint and No Moving Parts
FRC PFR flocculators are engineered with static inline mixers. This unique design reduces the inline pipe size for a short duration to achieve the required mixing action. As an added benefit, FRC PFRs have a compact footprint to save valuable facility space.
Forming “Flocs”
A coagulant is dosed to destabilize colloidal particles. This forms micro-flocs or pin-flocs. A flocculant is dosed to agglomerate the micro-flocs forming robust macro-flocs. The two key factors in this process are proper mixing and maintaining the integrity of the floc.
To achieve proper mixing, FRC flocculators use short, static inline static mixing zones. We reduce and expand the pipe diameter over a short pipe run in the reactor piping: one zone right after coagulant and caustic/acid addition and the other after flocculant addition. This accelerates the flow-through velocity and disperses the chemicals in and immediately after the mixing zone.
The FRC engineered design uses wide-radius bends instead of 90-degree elbows. Unlike the tight 90-degree elbows, these wide-radius bend do not shear flocculated solids after they have been formed. This allows for the formed flocs to coalesce into larger, fluffier particles over the rest of their retention time in the flocculator. By not shearing flocculated solids after they are formed, less chemicals are needed to achieve the desired level of separation and clarification.
Air Injection Ports
The air injection ports introduce micro-bubbles into the flocculator. This entrains air into the flocs from the beginning for easy separation upon entering the DAF.
Visual Inspection of Wastewater Throughout the Process
Sample ports are strategically placed throughout the flocculator to examine the changing water structure at each chemical dosage step. These ports show the wastewater at these points:
Raw wastewater
Coagulation and pH adjustment
Flocculation
DAF whitewater injection
Materials of Construction
PFRs can be constructed of:
HDPE
PVC / CPVC
SS304 / SS316
CSTRs can be constructed of:
FRP (single-chamber tank)
SS304 / SS316ti / Duplex SS (dual-chamber tank)
Complete Flocculator Systems
Flocculator applications can be enhanced with auxiliary equipment such as:
Chemical dosing pumps
Flow instrumentation
Control panels including PLC & HMI-rated NEMA 4X (SS304 enclosure)
CSTR Flocculator Features
Continuous-stirred tank reactors are tanks with mixers and can be used in lieu of a plug flow reactor. These allow you to:
Reduce the impact of continuous wide swings in flow rates
Increase residence time for the coagulation/flocculation process due to slow reaction kinetics
Produce not enough static head available to feed the DAF System